giobbi
Veteran Member
Forget Lucifer, Commodore socket is evil :D
I had a lot of issues related with the Commodore sockets, especially (but not only) the PET sockets. Contact cleaner, alcohol etc. don't solve: sometimes the problem is mechanical: loosen clips that make bad or no contact at all. So, when I'm having some trouble and there's a socket involved, my first move is to replace the socket with a good one.
----
I have a chiclet PET with 6550 RAM, that has a slightly bigger pitch respect the normal ICs like 2114. I cannot find an appropriate socket with the right size. Maybe some on-line shop like Mouser etc. sells them, but the shipping fees to Brazil are absurdly expensive.
After analyzing the original socket, I decided for a McGyver DIY fix (of course I had a B plan, but luckily I didn't need it).
The 6550 socket, at least the ones I had, were made in two part glued together: I opened them with a blade.
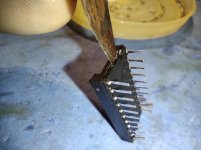
Then I removed the pins: I kept the shell and thrown the cover:
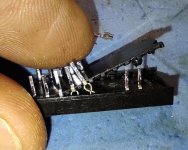
some precision sockets were the pin donors: it's just a matter to warm them, melting the plastic case, and push them out of the shell.
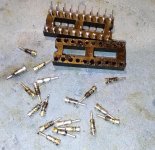
then I took and old, broken C=64 board as workbench and I put every pin into the 6550 shell, just pushing them through the hole.
Note: the lower part of the shell (the one that was turned to the PCB) now it's the upper part that will receive the IC.
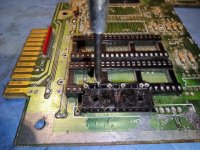
One row is done: time to do the other row.
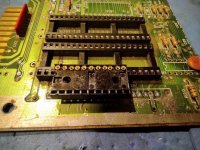
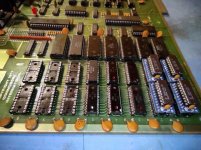
And finally all the sockets are succesfully soldered in the board. No more bad contact on my RAM ICs!
Note the 2114 -> 6550 adapter. I still have eighteen 6550 RAM chips working, but I'm going to preserve them, using the (expendable) 2114 RAM instead.
The 2114 -> 6550 adapter was made using the D'Asaro's schematics: a local pcb factory did them for me using the schematics with a little mod: I can now use a normal hair pin connector instead of the personalized pins of the original design. I just mounted 6 (the four in the picture + the two video RAM), I'm going to build all, but the smd chip is quite bad and bother to solder, so I'm doing a couple at a time ;-)
It took me about 6 hours to remove, rebuild and solder back the eighteen sockets (16 RAM + 2 video RAM). I did two at a time, testing them before to jump to the next two.
I had a lot of issues related with the Commodore sockets, especially (but not only) the PET sockets. Contact cleaner, alcohol etc. don't solve: sometimes the problem is mechanical: loosen clips that make bad or no contact at all. So, when I'm having some trouble and there's a socket involved, my first move is to replace the socket with a good one.
----
I have a chiclet PET with 6550 RAM, that has a slightly bigger pitch respect the normal ICs like 2114. I cannot find an appropriate socket with the right size. Maybe some on-line shop like Mouser etc. sells them, but the shipping fees to Brazil are absurdly expensive.
After analyzing the original socket, I decided for a McGyver DIY fix (of course I had a B plan, but luckily I didn't need it).
The 6550 socket, at least the ones I had, were made in two part glued together: I opened them with a blade.
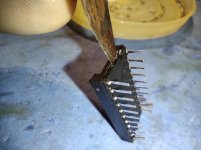
Then I removed the pins: I kept the shell and thrown the cover:
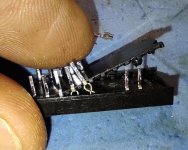
some precision sockets were the pin donors: it's just a matter to warm them, melting the plastic case, and push them out of the shell.
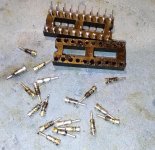
then I took and old, broken C=64 board as workbench and I put every pin into the 6550 shell, just pushing them through the hole.
Note: the lower part of the shell (the one that was turned to the PCB) now it's the upper part that will receive the IC.
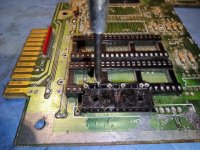
One row is done: time to do the other row.
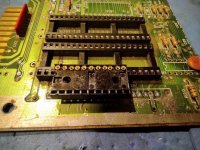
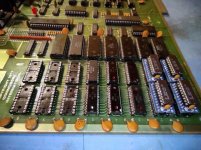
And finally all the sockets are succesfully soldered in the board. No more bad contact on my RAM ICs!
Note the 2114 -> 6550 adapter. I still have eighteen 6550 RAM chips working, but I'm going to preserve them, using the (expendable) 2114 RAM instead.
The 2114 -> 6550 adapter was made using the D'Asaro's schematics: a local pcb factory did them for me using the schematics with a little mod: I can now use a normal hair pin connector instead of the personalized pins of the original design. I just mounted 6 (the four in the picture + the two video RAM), I'm going to build all, but the smd chip is quite bad and bother to solder, so I'm doing a couple at a time ;-)
It took me about 6 hours to remove, rebuild and solder back the eighteen sockets (16 RAM + 2 video RAM). I did two at a time, testing them before to jump to the next two.